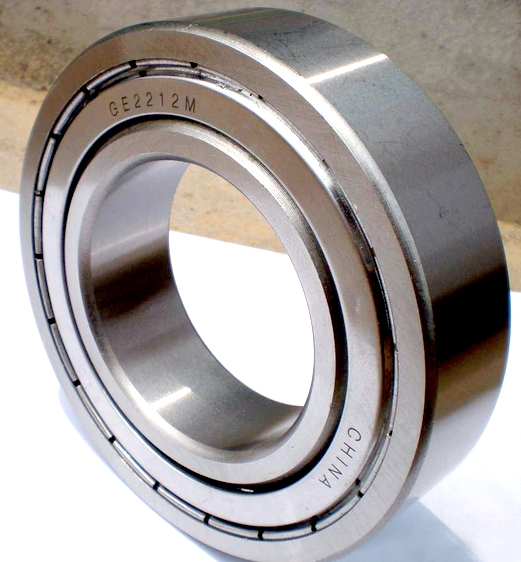
制定轴承更换周期需结合设备特性、运行工况及维护数据,通过科学评估实现预防性维护。以下是制定周期的关键步骤和考量因素:
### 一、基础参数分析
1. **设备类型**:明确轴承应用场景(如电机、泵机或重载设备),参考制造商建议的MTBF(平均无故障时间)作为基准周期。
2. **负荷特性**:统计实际载荷(恒定/冲击载荷)、转速(高速轴承寿命通常缩短30%-50%)及每日运行时长,结合ISO 281标准计算理论寿命。
### 二、动态监测指标
1. **振动分析**:安装在线监测系统,当振动值超过ISO 10816标准阈值(如加速度>4m/s²)时触发预警。
2. **温度监控**:持续记录轴承温度,异常升温(超过环境温度40℃)可能预示润滑失效或磨损加剧。
3. **润滑状态**:通过油液光谱分析检测金属颗粒浓度,铁元素含量突增50%以上需提前更换。
### 三、环境修正系数
1. **污染等级**:在粉尘环境(如矿山)中,轴承寿命需按DIN标准乘以0.6-0.8的修正系数。
2. **温湿度影响**:高温(>80℃)环境需采用特殊润滑脂,湿度>80%时周期缩短20%。
### 四、维护策略制定
1. **定期更换**:对关键设备执行强制更换(如每12-18个月),配合大修周期实施。
2. **状态维修**:建立设备健康档案,当累计运行8000小时或出现3次预警后强制更换。
3. **经济性评估**:对比预防性维护成本与故障停机损失,优先保障连续生产设备。
### 五、持续优化机制
每季度分析故障数据,利用威布尔分布模型优化周期参数,允许±15%的调整幅度。通过PDCA循环实现周期动态管理,典型行业更换周期参考:风电主轴轴承3-5年,机床主轴轴承2-3年,输送辊道轴承6-12个月。
该方案可降低30%以上意外停机风险,同时避免过度维护造成的资源浪费。